
EN ESTE TEXTO SE PUEDE CONSULTAR LOS SIGUIENTES TEMAS:
INTRODUCCIÓN
CARDAR
HISTORIA
CURIOSIDAD
EL PROPÓSITO DEL CARDADO
PARTES PRINCIPALES
MATERIAL ENTRANTE
PUNTOS DE VISTA EN EL CARDADO
ALIMENTACIÓN POR NAPAS EN ROLLO (LAPFEEDING)
LA ALIMENTACIÓN DE FLOCK
TIPO DE ALIMENTACIÓN DE FLOCK (FEED CHUTE)
TAKER-IN
LIKER-IN
REGLAS DEL CARDADO
FLUJO DE CARDA
SUBPRODUCTO
CHEQUEOS
PRODUCCIÓN ESPERADA POR TIEMPO
DINÁMICA DE LAS FIBRAS EN LAS CARDAS. CHAPONES, UNA INVERSIÓN CRÍTICA
Figura: Distribución de la masa de fibras durante el cardado de fibra corta.
FUNCIONES DEL OPERARIO
CONTROL DE CALIDAD EN EL CARDADO
BIBLIOGRAFÍA
INTRODUCCIÓN.
"El cardado es el corazón de la hilandería"
"El buen cardado es la mitad del hilado"
"El buen cardado es la mitad del hilado"
“El cardado es el corazón de la hilandería, un buen cardado es la mitad del hilado”; estos proverbios no dan una idea de la enorme trascendencia del cardado en el proceso de producción. La alta producción en el cardado para economizar el proceso conduce a una reducción en la calidad del hilo. En una producción mayor, lo más sensible se convierte en la operación de cardado y un mayor peligro de influencia negativa en la calidad.
Los cambios tecnológicos que han tenido lugar en el proceso de cardado son notables. Las máquinas más modernas alcanzan una tasa de producción de 60 a 100 kgs / h, que solía ser de 5 a 10 kg / hr hasta1970.
CARDAR:
Peinar con fuerza las fibras textiles antes

El CARDADO es el proceso posterior a la apertura, siendo ésta de vital importancia para el mismo, siendo la carda la primera máquina en la preparación de nuestra hilatura. El cardado que consiste en la transformación de las fibras textiles en mechas de aproximadamente cuatro centímetros de diámetro las cuales se enrollan hasta una longitud de aproximadamente 5,000 metros. El Cardado es un proceso mecánico que rompe los grupos no organizados de fibras (enmarañamientos de la misma) y alinear las fibras individuales de manera que sean más o menos paralelas entre sí. (2)
HISTORIA.
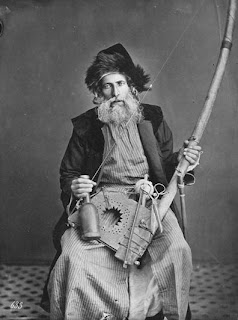
El historiador de ciencia Joseph Needham se atribuye la invención del instrumento del arco utilizados en la tecnología textil en la India. Las primeras pruebas del uso de instrumentos de arco para el cardado viene de la India (2do siglo dC). Estos dispositivos de cardado, llamado “Kaman” y la “dhunaki” hacen que se afloje la textura de la fibra por medio de una cuerda vibrante.
En 1748, Lewis Paul de Birmingham, Inglaterra inventó la hand driven carding machine. Una capa de alambre fue colocada alrededor de una carda que fue envuelta alrededor de un cilindro. Daniel Bourn obtuvo una patente similar en el mismo año, y probablemente lo usó en su fábrica de hilado en Leominster, pero ésta se incendió en 1754. La invención más tarde fue desarrollada y mejorada por Richard Arkwright y Samuel Crompton. Una segunda patente fue la de Arkwright (1775) para su máquina de cardar; posteriormente fue declarada nula, ya que carecía de originalidad.

Desde la década de 1780, las máquinas de cardado se establecieron en las fábricas en el norte de Inglaterra y Gales. La primera en el País de Gales se encontraba en una fábrica en Dolobran cerca Meifod en 1789. Estos molinos producían hilo cardado en particular para la industria de la franela de Gales.

CURIOSIDAD
El cardado de la lana se puede hacer "en la grasa" o no, dependiendo del tipo de máquina y de la preferencia del girador. "En la grasa" significa que la lanolina que naturalmente viene con la lana no ha sido lavada, dejando la lana con un tacto ligeramente graso. El gran tambor cardador no tiende a llevarse bien con lanolina. Una ventaja importante de trabajar con la lanolina todavía en la lana es que deja al trabajador con las manos suaves. (3)
EL PROPÓSITO DEL CARDADO.
- Abrir los flocks en fibras individuales.
- Limpiar y eliminar impurezas.
- Reducción de neps.
- Eliminación de polvo.
- Eliminación de fibras cortas.
- Mezcal de fibras.
- Orientación y alineación de fibras.
- Formación de felpa (afelpado).
El rollo de napa es transformado en velo en la parte delantera de la máquina, comprimiéndolo posteriormente para dar origen a una cinta de masa por longitud estándar y debidamente dispuesta.
En el cardado se cumplen las siguientes funciones:
- Alimentación por medio de un rollo de napa o alimentación directa a la carda sin
- formación de rollo (sistema moderno).
- Continuación de la apertura y limpieza del material.
- Individualización de las fibras (cardado propiamente dicho).
- Condensado de las fibras para formar un velo.
- Desprendimiento del velo y posterior condensado del mismo para formar una cinta con determinado peso por unidad de longitud.
- Devanado de la cinta en un bote.
- En la zona de apertura y limpieza se extrae el subproducto conocido como “carcomo”.
- Al final de la zona de cardado se extrae el subproducto.

1 - Gran cilindro.
2 - Cadena de chapones.
3 - Cepillo limpiador de chapones.
4 - Cilindro desprendedor.
5 - Doffer.
6 - Motor principal.
7 - Lickerin.
8 - Piñón de tensión trasero.
9 - Silos de la carda.
10 - Mesa de alimentación.
2 - Cadena de chapones.
3 - Cepillo limpiador de chapones.
4 - Cilindro desprendedor.
5 - Doffer.
6 - Motor principal.
7 - Lickerin.
8 - Piñón de tensión trasero.
9 - Silos de la carda.
10 - Mesa de alimentación.
MATERIAL ENTRANTE.
La materia prima, previamente mezclada, los cuales deben reunir todos los requisitos de calidad necesarios para su procesamiento, garantizando así un buen suministro de materia prima en el proceso de cardado, facilitando además la labor para los procesos siguientes, mediante la obtención de una cinta de óptima calidad.
MATERIAL SALIENTE.
El material saliente de la carda es una cinta de buena calidad la cual debe cumplir con los siguientes requisitos:
- Que no contenga tramos gruesos y/o tramos delgados.
- Que la cinta no esté contaminada de ningún tipo de grasas o aceites, además que no haya borra adherida al material.
- El bote no debe pasar de su capacidad normal de llenado, evitando así que el material se caiga al piso.
- En todos los turnos se realiza por parte del mecánico un chequeo de producto entregado para garantizar que la cinta sea uniforme y salga con un peso por Yarda requerido.
- Realizar chequeos de uniformidad en USTER y chequeo de neps por pulgada para garantizar que el producto final (cinta) salga con buena calidad.
- La cinta sale con un peso irregular yarda por yarda ya que la carda no tiene un sistema de regulación efectivo.
- Las fibras salen desordenadas y con una textura áspera, y con una mínima presencia de impurezas.
- La cinta producida por la carda es depositada en botes plásticos de 40 pulgadas de diámetro por 42 pulgadas de altura, tienen una capacidad de 50 kilogramos, y le caben 9500 metros de cinta.
PUNTOS DE VISTA EN EL CARDADO.
1. La alimentación del material en forma de napa (the form of scutcher lap).
2. Sistema de alimentación de flock (los flocks son transportados neumáticamente).
Alimentación por Napas en rollo (lapfeeding)
1. La densidad lineal de la vuelta es muy buena y es más fácil de mantener (uniformidad).
2. Toda la instalación es muy flexible (se puede mover para donde se desee a diferencia del blowroom).
3. Las desviaciones en la salida de la carda será igual a cero, así como las vueltas pueden ser rechazadas.
4. Los auto niveladores no son necesarios, por lo tanto, los costes de inversión y mantenimiento son menores.
5. La transportación de vuelta necesita de más esfuerzo manual (más mano de obra).
6. La napa puede ser un daño extra y se puede cambiar.
7. Más pérdida de fibras durante su vuelta de cambio (lap change).
8. Más carga sobre el taker-in; puede ser más pesada y muy comprimidas.
La alimentación de flock
1. Alto rendimiento en el cardado debido al alto grado de apertura de la red alimentadora.
2. La necesidad de trabajo es menor debido a que no transporta de vuelta y vuelta en el cambio de cardado.
3. La alimentación de flocks es la única solución para la alta producción de cardado.
4. La densidad lineal de la red de alimentación de la carda no es tan buena como la napa.
5. La instalación no es flexible.
6. Los autoniveladotes son una necesidad, por lo tanto, los costes de inversión y costo de mantenimiento con mayores.
Tipo de alimentador de flock (feed chute)
1. Hay dos conceptos básicos de alimentador de flocks:
1) Una tolva sin un dispositivo de apertura.
2) Dos tolvas con un sistema de apertura.
2. La de una es más simple, económico y requiere poco mantenimiento.
3. La de dos tolvas es compleja y costosa.
4. El de una tolva es un sistema cerrado, vuelve exceso de tocks a la distribuidora, si hay demasiado material presente, los NEPS pueden aumentar.
5. El de una tolva no es flexible para ejecutar diferentes mezclas.
6. Las restricciones de diseño son más con la de una sola tolva.
• Un dispositivo de alimentación es una necesidad para alimentar a la red alimentadora de la región taker-in y debe realizar las siguientes tareas:
1. Fijar el batt de forma segura en toda su anchura.
2. Adherir las fibras herméticamente sin deslizamientos durante el taker-in.
3. Presentar las fibras de tal manera que la apertura se puede realizar con suavidad.
TAKER-IN
• El diversificador de nariz (The divertor nose) (agudo o redondo) y la longitud de la nariz (la superficie de un guía) tienen una influencia significativa en la calidad y la cantidad de residuos eliminados. El Shart nose divertor evita el deslizamiento de fibras, pero la acción de apertura no es suave. Si la longitud de la superficie de guía es demasiado corta, las fibras pueden escapar a la acción de la taker-in. Que se raspan por los cuchillos de mota y se pierden en el receptor de los residuos.
• El Rodillo de alimentación vestido de sierra dentada, es siempre mejor, porque le da la retención de batt buena. Así, el efecto de apertura del taker-in es más como en la cardadura.
• Rieter ha desarrollado un "sistema de alimentación unidireccional", donde los dos dispositivos de alimentación (rodillo de alimentación y la placa de alimentación) son dispuestos en sentido opuesto cuando se compara con el sistema convencional. Es decir, el cilindro se encuentra debajo de la placa y se presiona contra el cilindro por la fuerza de resorte. Debido a la dirección del rodillo de alimentación, el batt de fibra se extiende hacia abajo sin desviación directa en los dientes del taker-in (lame-in) que resulta en el tratamiento de fibra suave. Esto ayuda a reducir las fallas en el hilo.
• El propósito del taker-in es guiarlos en la partes de eliminación de suciedad como cuchillos de motas, segmento de cardado y placas de residuos, y después de entregar las fibras a los principales cilindros. En el cardado de producción alta, los rangos de velocidad rotacional son de 700-1400.
• El tratamiento para la apertura y limpieza impartida por Taker-in es muy intensa, pero desafortunadamente no es muy gentil. Hay que recordar que alrededor del 60% de las fibras que alimentan al cilindro principal está en forma de fibras individuales.
• La velocidad circunferencial del taker-in es de alrededor de 13 a 15 m / seg. Esto claramente muestra que la fibra se ha deteriorado a este punto de apertura. El grado de deterioro puede ser controlado sólo mediante el ajuste de lo siguiente:
1. El espesor de la batt.
2. El grado de apertura del material en crudo (rawmaterial).
3. El grado de orientación de las fibras.
4. La agresividad de la vestidura.
5. La distancia entre los dispositivos.
6. La velocidad de rotación del taker-in.
7. El rendimiento del material.
LIKER-IN
Las últimas cardas de TRUTZSCHLER trabajan con tres likers-ins en comparación con un único liker-in. El primero se construye como un rollo de aguja. Esto se traduce en una apertura muy suave y una vida muy larga de la vestidura para este rollo. Los otros dos rodillos son para vestiduras más fina y más altas velocidades, lo que resulta en un porcentaje de alimentación mayor de fibras individuales y pequeños mechones en comparación al de licker-in único, el cilindro principal. Esto permite que el cilindro principal vaya en alta velocidad y reduce la carga sobre el cilindro y las tapas planas. No por una mayor productividad se logra con buena calidad. Sin embargo, el rendimiento puede variar según los diferentes materiales y los niveles de residuos.
Entre el taker-in y en cilindro principal o tambor, las vestiduras están en la disposición de quitarse. Ejerce una influencia en la calidad de la cinta y también en la mejora de la orientación de las fibras longitudinales que se produce aquí. El efecto depende del draft entre el cilindro principal y taker-in. El draft entre el cilindro principal y el taker-in debe ser un poco más de 2.0.
El efecto de la apertura es directamente proporcional al número de puntos de cable por fibra. En el taker-in tal vez en 0,3 puntos / de fibra y en el cilindro principal 10-15 puntos / fibra. Si una determinada calidad de hilo requiere un grado correspondiente de la apertura de la carda necesaria. Para aumentar la producción en el cardado, el número de puntos por unidad de tiempo también debe ser aumentado. Esto puede lograrse a través de:
1. Más puntos por unidad de área (ropa fina).
2. Altas velocidades de rodillos y cilindros.
3. Más superficie y mayor posición de cardado.
Por lo tanto la mejor forma es añadir la superficie de cardado (piso estacionario). Las placas del cardado pueden aplicar en:
1. En el marco del Liker-in.
2. Entre los licker-in y pisos.
3. Entre pisos y doffer.
Taker-en no entregar las fibras individuales de 100% al cilindro principal. Ofrece alrededor de 70% en pequeñas bandadas al cilindro principal. Si los segmentos de cardado no se utilizan, la carga en el cilindro y pisos será muy alto y cardado de la acción también sufre. Si se utilizan segmentos de cardado, garantizan una mayor apertura, adelgazamiento y, principalmente una mejor distribución de los flocks por la superficie total de área. Los segmentos cardantes traen las siguientes ventajas:
1. Mejora de la suciedad y la eliminación de polvo.
2. Mejor desenmallaramiento de motas.
3. La posibilidad de aumentar la velocidad (aumento de la producción).
4. La preservación de la vestidura.
5. La posibilidad de usar vestiduras más finas en los chapones y en el tambor.
6. Una mejor calidad de hilados.
7. Menos daño a la vestidura.
8. Vestiduras limpias.
El trabajo principal del cardado, se da en la separación de las fibras individuales que se realizan entre el cilindro principal o tambor y los chapones. Sólo por medio de esta separación de fibras, es posible eliminar las partículas de suciedad y el polvo fino.
Cuando el chapón entra en la zona de trabajo, que se llena muy rápidamente. Una vez que se llena, después de unos pocos segundos, a partir de entonces, se produce mayor asimilación de las fibras, sólo cardando. Acorde a esto, si un haz de fibras no se encuentra bien paralelizada en el lugar de los chapones, entonces se trabajará con gran dificultad. Esto se extenderá entre las superficies de trabajo y por lo general conduce a la formación de neps.
En principio, los chapones se pueden mover hacia delante o hacia atrás, es decir, en la misma dirección o en la opuesta al tambor. En el movimiento inverso, los chapones de entrar en relación de cooperación con la vestidura del cilindro de prendas en el lado del doffer. En esta etapa, los chapones están en condiciones de limpieza. A continuación, avanzan hacia la el taker-in y se llenan durante este momento. Parte de su capacidad de recepción es lo que perdió, pero sigue siendo suficiente para la eliminación de la suciedad, ya que este paso tiene lugar cuando el material entra por primera vez los chapones.
En esta posición, por encima del taker-in, el cilindro lleva el material de limpieza en los chapones. Este último toma la tierra. En cambio, la suciedad se quita inmediatamente de la máquina. Estudios de RIETER muestran claramente que la mayor parte de la suciedad es lanzada primero en los chapones, directamente por encima del taker-in.
Kaufmann indica que el 75% de todas las motas pueden ser desintegradas, y de esto el 60% son de hecho desintegradas.
La disposición de las prendas de vestir entre el cilindro y el doffer no es para la extracción de acción, es para la ACCIÓN DEL CARDADO. Esta es la única manera de obtener una acción de condensación y, finalmente, a formar una red. Tiene tanto ventajas y desventajas. La ventaja es que la acción de cardado adicional se obtiene aquí y se diferencia un poco del proceso de los chapones.
Hay dos reglas de cardado:
1. La fibra debe entrar en la máquina de cardado, de manera eficiente cardado y tomado de ella en el menor tiempo posible.
2. La fibra debe estar bajo control de la entrada a la salida.
El efecto Cardante está teniendo efecto entre el tambor y doffer porque, ya sea la vestidura del tambor a través de las fibras atrapadas en la vestidura del doffer, o la vestidura del doffer y las fibras atrapadas en el tambor.
Los neps todavía se pueden separar aquí, o no separadas por paquetes de fibras pueden ser abiertas un poco en este ámbito y pueden ser separados durante el paso siguiente a través de los chapones.
FLUJO DE CARDA.

- Cojín o borra: desperdicio producido por la carda: de cascarilla, semilla, fibras enredadas, tabaquillo, pedazos de hoja.
- Chapón: Desperdicio generado por la acción de los chapones sobre el gran cilindro retirando fibras cortas y micro polvo.
- Cinta y velo: Desperdicio producido por los revientes de la cinta y al emparejar la carda, este material es reutilizado.
CHEQUEOS.
Al material saliente de la carda se le hacen los siguientes chequeos:
- Chequeo de peso. Se toma una muestra de cinta, se mide y luego se pesa para verificar si cumple con un estándar de peso por longitud.
- CV: coeficiente de variación reportado por el USTER.
- Chequeo de neps. Para el chequeo de neps se toma una muestra de 100g y se observa en la lupa para contar los neps, se compara con los estándares, para saber si la cinta cumple con los requisitos de calidad y si no los cumple se deben hacer ajustes a la carda.
PRODUCCIÓN ESPERADA POR TIEMPO.
La producción esperada depende de tres variables: la velocidad de la máquina, el peso de la cinta y el tiempo de trabajo de la máquina.

NORMAS DE SEGURIDAD.
Si el operario nota cualquier ruido extraño en la Carda y cualquier defecto en las piezas, de inmediato inactiva la Carda y le informa al mecánico.
No utilice anillos, cadenas, ni relojes ya que le pueden ocasionar un accidente.
EQUIPO DE PROTECCION PERSONAL.
Estos son usados para prevenir enfermedades profesionales o accidentes.
- Protección Auditiva: Debido al alto ruido producido por las diferentes máquinas existentes en el salón de preparación hilados (cardas, estiradoras, mecheras, hiladoras). Es indispensable usarlos ya que pueden ocasionar daños irreversibles en el oído.
- Respiradores Desechables: Estos son utilizados como prevención, ya que el ambiente tiene muchas partículas que pueden llegar fácilmente a los pulmones produciendo muchas enfermedades.
- Estuche para el cuchillo: con el constante trajín del operario el cuchillo debe de llevarse en su respectivo estuche para evitar así un accidente.
En los últimos 30 años numerosos acontecimientos han tenido lugar en el cardado del algodón. La tasa de producción se ha incrementado por un factor de 5 con los principales componentes de rotación a velocidades significativamente más altas.
Los rodillos de taker-in, con modificaciones, sistemas de alimentación están en uso, los segmentos adicionales de la carda están equipados para más apertura de la fibra efectiva, y la mejora del alambre de las vestiduras ha sido desarrollada para una mejor acción de cardado. Los avances en electrónica han proporcionado mucha mejorar el seguimiento y control de procesos. La mayoría de estos desarrollos han dado lugar a una mayor limpieza de fibras de algodón, neps reducidos en el velo de la carda y mejorar la uniformidad de la cinta.
A pesar de las mejoras que se han hecho en las cardas, una opinión generalizada es que se sepa más sobre los procesos de limpieza en la carda que sobre el proceso de cardado en si. Por ejemplo las cardas actuales pueden lograr una eficiencia de limpieza general del 95%. Está bien establecido que la eficacia de la limpieza de los modernos sistemas de taker-in es de alrededor del 30%.
Sin embargo, aunque el contenido de neps y la cinta Uster CV% se utilizan como medidas de calidad del rendimiento del cardado que no son indicadores satisfactorios para adelantarse a la calidad del hilado. Esto se debe a que algunos arreglos en la cinta de fibra puede conducir a la formación de neps e imperfecciones.
Además de la eliminación de basura y motas, algunos aspectos importantes del proceso de cardado, en relación con la calidad del hilado y el rendimiento de spinning, son el grado de individualización de fibra, en la medida en fibra y las configuraciones del gancho de fibra en la cinta. Con respecto a estos factores, el aumento de la tasa de producción puede reducir la calidad de cardado. Por tanto, es de importancia que una mejor comprensión está establecida que el efecto de las acciones del cardado tengas sobre los parámetros de calidad, sobre todo en tasa de producción alta.
El punto de vista más ampliamente aceptado de cómo las fibras se distribuyen dentro de la carda en condiciones de estado estacionario se ilustra en la Figura 1. Los estudios reportados en los fundamentos del proceso de cardado han sido, en gran medida, de forma en que se trate los componentes principales de trabajo de la carda, afecten a esta distribución de la masa de fibras e interactúen con la masa para lograr: remover desperdicios y neps del algodón; el desenmarañamiento de la masa de fibras en fibras individuales con rotura de fibras mínima, y la alineación de las fibras para dar una cinta adecuada para el estiraje en los procesos siguientes. (7)
Estas acciones se producen en la interfaz de los componentes de carda en las tres zonas que se indican en la Figura 1. (5)

Q1: masa de fibra es transferida del cilindro para doffer.
K: coeficiente de transferencia.
Q2: Capa de reciclaje.
QL: masa de fibras transferida del taker-in al cilindro.
Qf: tiras de los chapones.
Qo: Capa de funcionamiento.
(Donde Q es la masa por unidad de tiempo)

FUNCIONES DEL OPERARIO.
1. Cambiar los contadores: El operario toma en orden lógico y verifica que sí esté funcionando bien el contador. Además, efectúa las siguientes revisiones: automáticos delanteros, el ducto de la cubierta del doffer y retira los tacos si los hay (con máquina parada).
2. Limpiar el equipo: Al iniciar turno paran las cardas; con la ayuda del mecánico de sección y el limpiador, realiza ventilada general a cada carda con manguera de aire; cada dos horas un Operario indirecto toma el desperdicio los palos limpia chapón y lo recoge.
3. Emparejar la Maquina: Después de cambiar los contadores y limpiar las maquinas, el operario espera a que llegue el material. El material ingresa a cada carda y se va enhebrando automáticamente hasta que sale el algodón convertido en velo.
4. Colocar en funcionamiento y Corregir Paros en la Carda: El Operario acciona la perilla de baja velocidad, espera que salga el velo Forma una Cinta, la “torsióna” hasta formar una punta, luego la introduce por las boquillas de la zona de estiraje; continúa con la punta de la cinta hasta la boquilla del Coiler se asegura que la punta salga, y hace el empate de la cinta. Luego activa la velocidad alta, recoge el desperdicio de velo y cinta y echa al bote respectivo. Si se presenta un paro en cualquier partes de la carda como Cilindro y cuchillas, Zona de estiraje, Cilindros y coberturas, Atranque en Lickerín y Paros en falso, se retiran las partes implicadas para corregir el paro y se repite el proceso de arranque de la maquina.
5. Patrullar y corregir paros: Recorre el área y atiende los paros que le indique la torre de luces. Además observa que la cinta se esté enrollando correctamente, y que la carda se este alimentando en forma correcta.
CONTROL DE CALIDAD EN EL CARDADO.
Se refiere a los defectos que pueden obtener en la producción del velo o cinta por causas principalmente mecánicas, inapropiados ajustes, velocidades inadecuadas.
Esta máquina requiere de un constante mantenimiento preventivo buscando evitar el correctivo, ya que éste último, es más caro porque detiene por lo menos en más de un turno. Por ello se recomienda, en cardas convencionales: limpieza en cada turno, vaciado de cajas de impurezas, retirado del “chapón” (se denomina chapón o hueso al desperdicio de fibra demasiado cortas), limpieza de residuos vegetales, etc. Que han quedado atrapados en los dientes de los chapones de manera semanal o mensual. Según el grado de limpieza de la fibra, abrir tapas para limpiar guarniciones, tambor, gran tambor y doffer. Cada cierto periodo afinar esmeril o cambiar guarniciones. El lubricado y engrasado de rodamientos deberá efectuarse diario.
1.- Velo de cinta irregular. Generado en base al número por ajustes inadecuados que tenga, se dará entre:
a) Mesa de alimentación y tomador.
b) Tomador y rejillas.
c) Entre gran tambor y chapones. O bien una guarnición del gran tambor y/o chapones gastados. Por guarniciones demasiado bajas debido a que están demasiado afilados o esmerilados. Por napa de alimentación irregular, por movimiento irregular de los chapones, etc.
2.- Velo nublado. Se entiende por nublado a las partes o porciones con mayor cantidad de fibras debido a un estiraje excesivo en la zona de alimentación. Se da cuando el gran tambor y el doffer no son perfectamente cilíndricos, por esmerilados o afilados mal hechos, por un ecartamiento más abierto entre tomador y gran tambor y entre este y el doffer. También se da por acumulaciones de fibras en algunas partes de los cilindros que se desprenden de manera irregular adhiriéndose al material en proceso.
3.- Velo que rompe mucho o no se separa fácilmente. Debido a condiciones ambientales inadecuadas (mayor humedad de la requerida), por velocidad y/o ecartamientos inadecuados del peine o crossroll, además de obstrucciones en el depósito condensador que impiden una correcta fluidez del material.
4.- Velo recortado en sus orillas. Por napas de alimentación irregulares, por rejillas demasiado abiertas, por acumulaciones de impurezas, residuos de grasa o acumulaciones de fibras en las orillas del cilindro o los chapones.
(6)
BIBIOGRAFÍA.
- http://es.thefreedictionary.com/cardado
- http://primavera2010manufactura.googlegroups.com/web/CARDING.pdf?hl=es&gda=OZfoX0EAAAAFkHQo47C2JmxZ4JqeRkrRibKzwh2A8cGYWOqxGtHqeFgZCRY815cWNZVVlAqAbm-9LBFaaGh5CE6dZP4UoZa2CauILEPedMr94Qv9KiIH-A
- http://cl.kalipedia.com/kalipediamedia/historia/media/200707/17/hisuniversal/20070717klphisuni_68.Ges.SCO.png
- http://en.wikipedia.org/wiki/Carding
- http://josemaldonadoingenieriatextil.blogspot.com/search?updated-min=2009-01-01T00%3A00%3A00-08%3A00&updated-max=2010-01-01T00%3A00%3A00-08%3A00&max-results=1
- Carding.
- Apuntes de Hilatura 1.
- PROCESS+PARAMETERS+IN+CARDING
muy bueno, un saludo de Perú
ResponderEliminarHola , soy mecánico industrial y estoy tomando mi primer contacto con las cardas, esta información me resulto muy útil !muchas gracias por compartirla. un saludo desde Uruguay.
ResponderEliminarExelente imformacion me sera muy util.Gracias.
ResponderEliminar